Fatty-acid production
A higher degree of fat-splitting
With thermal fat splitting, you don’t just achieve a higher level of splitting – you also increase capacity while saving on energy and water use
Save up to 30% on energy and water usage
As a fatty acid producer, achieving a 99% degree of splitting is one of your primary goals—but you have to balance that against challenges like energy costs and water usage.
Novonesis Lipura® Split enzymatic Pre-Splitting Technology is easy to implement and helps you increase efficiency, sustainability, and profitability—with little or no CAPEX cost.
Thermal fat splitting: the current industry standard
Fatty acid is a building block for a wide variety of different products—from lubricants to foods.
In the thermal fat splitting process, fats and vegetable oils (triglycerides) are converted into fatty acids and glycerol using a high-pressure, high temperature process in a splitting tower.
Although thermal fat splitting is generally effective, throughput is slow, and requires a great deal of energy.
Triglyceride conversion happens in three stages. The first stage is slow as the water and fats mix. Most of the fat is split in the latter two stages. With our solution, you can expect to accelerate the rate of reaction in the first stage.
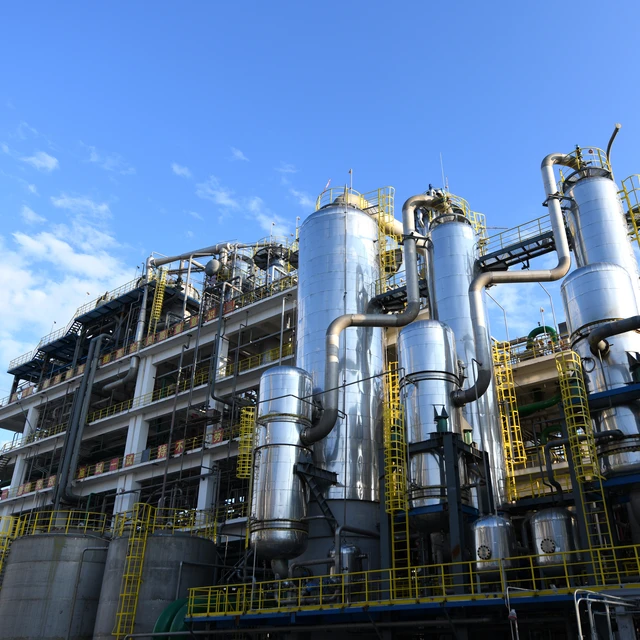
Improving the efficiency of thermal splitting
Pre-splitting makes thermal splitting far more efficient. Novonesis Lipura® Split—an enzyme biocatalyst—and water are added to feedstock in an existing stir tank and agitated prior to introducing the mix into the splitting tower.
This greatly reduces—or even eliminates—the initial stage of the thermal splitting reaction, making the process far more efficient by reducing the amount of energy required—all without little or no CAPEX investment.
Click on the video to learn more about how it works.

Benefits
Pre-splitting with Novonesis Lipura® Split boosts delivers a number of significant benefits in the thermal fat splitting process.
Up to 30% energy savings
By decreasing thermal splitting temperatures by as much as 30℃ without compromising the degree of splitting, high pressure steam consumption can be reduced by up to 30%
Higher degree of splitting
Trials show an increase of 0.5% on the degree of splitting (DOS) at the same temperature of the normal process
Increased throughput
Industrial trials show that flow can be increased by up to 20% while keeping the same DOS depending on the capacity of the fatty acid installation.
Up to 30% water savings
By substantially shortening/eliminating the initial phase, less water is required in the thermal splitting tower to achieve the same DOS.
Increase energy and water savings in your fat-splitting plant
If you’re looking for an innovative way to maximize the value of your feedstock and boost the profitability of your oleochemicals business, join our Novonesis experts in this on-demand webinar.
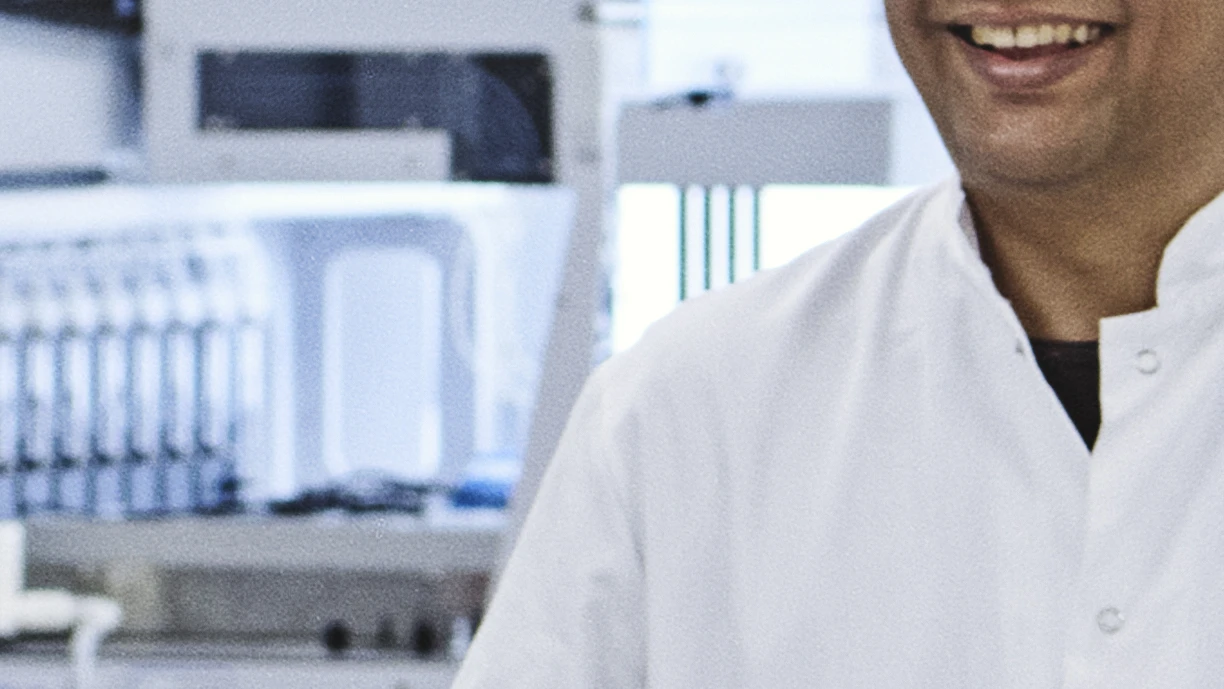
How can we help your business?
Fill in the form below and we’ll be in touch.
One more step…
To complete the get in touch form or sign up, please click on the button below to enable cookies.