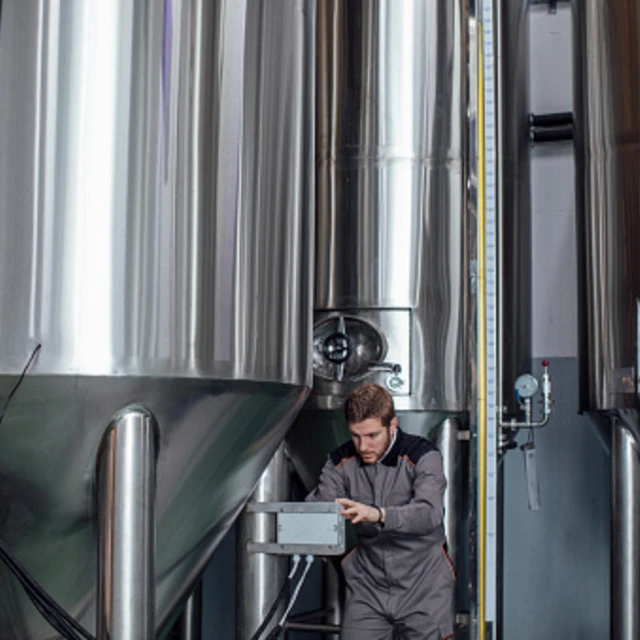
More CapEx or more optimal process?
Case study: Find out how enzymes helped this customer find more capacity by reducing the required occupancy time in the fermenter
Finding a cost-efficient way to boost volume was hard
An international brewer was capacity constrained in the fermentation/storage area. They needed to find capacity to increase volume and meet demand.
Fermentation required 7 days, of which 2-3 days were diacetyl rest, giving the yeast time to take up diacetyl and turn it into acetoin.
While the brewer could have expanded capacity with a large capital expenditure, high energy and raw material prices were already a challenge. It was much preferable to avoid further investments.
Maturex® Pro cuts fermenter time by 2 days
Novonesis Maturex® Pro helped reduce the required occupancy time of the fermenter by two days. Considering both fermentation, cooling and cleaning, the result was an estimated 15-20% reduction – a significant capacity release.
Maturex® Pro converts alpha-acetolactate (produced by the yeast) to acetoin. This avoids diacetyl. The customer measured diacetyl in spec when the beer attenuated.
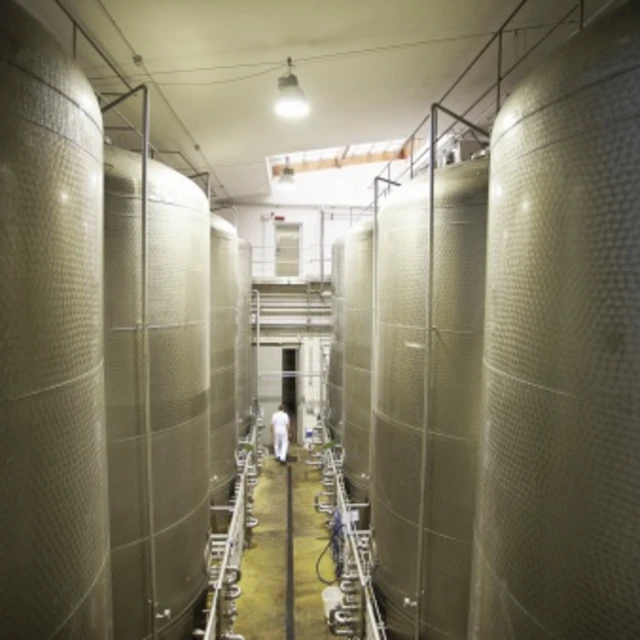
Proper application ensures enzyme effectiveness
Application is key to the success of the enzyme. In some cases, it needs to be “around” the yeast before the yeast produces alpha-acetolactate.
If there is a layering in the fermenter and the product was applied long after the yeast was pitched, the yeast releases alpha-acetolactate – which turns into diacetyl by spontaneous decarboxylation. Once diacetyl is produced, the yeast must take it up and convert it to acetoin.
Maturex® Pro only works on alpha-acetolactate.
Location: Europe
Explore more success stories.
Turning a ban into a boon
Challenge: The quality of raw materials varied significantly when imports of barley were banned in the country. A regional brewer experienced that both production efficiency and quality of finished beer products were affected.
3 X lower dosing rate cuts costs
Challenge: Production of a regional and international brewer’s ultra-low-carb beer used a glucoamylase that required a very high dose rate. This created unnecessarily high costs on multiple areas.
Filtration benefits far exceed enzyme cost
Challenge: A better wort and beer filtration process was needed at this regional brewer. For years, it had used a “traditional” beta-glucanase in its process.